Stope Mapping with Hovermap
Map stopes in minutes
Hovermap enables data capture of critical underground mine excavations, delivering new insights for mine planning and operations.
With Hovermap, mine and geotechnical engineers can easily map underground excavations—quickly, safely, and with minimal disruption to production.
TRADITIONAL CMS MAPPING
Cavity monitoring systems (CMS) are time-consuming, often requiring multiple scans that take hours—halting production. The boom-mounted scanner is extended out into the stope, requiring surveyors to work in close proximity to drawpoints or past a stope bund.
At drawpoints the surveyor is exposed to the risk of sudden rock fall and riling hazards, while access to upper levels of an open stope can expose them to unknown undercutting.
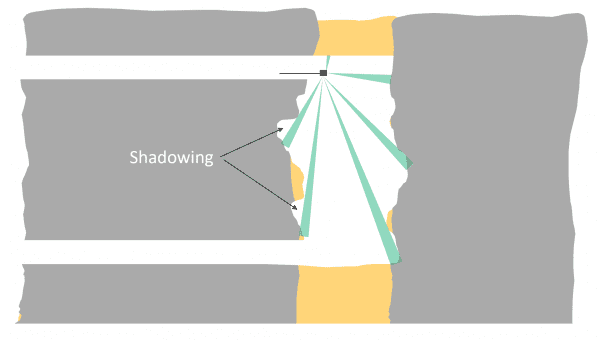
CMS imaging contains shadowing, occluded areas of a stope, and variable point density, reducing the value of the data for geotechnical, volumetrics or reconciliation analyses.
Substituting a CMS with a drone-mounted LiDAR scanner eliminates the requirement for surveyors to work near the stope edge, and improves data quality and coverage.
MAP HAZARDOUS AREAS SAFELY & QUICKLY
Hovermap is a drone-mounted mapping solution able to operate in GPS-denied and hazardous environments. Hovermap can fly a mission and within minutes capture high resolution LiDAR point clouds and imagery.
These data sets provide mining and geotechnical engineers with rock mass, structural and volumetric data of unparalleled quality — improving decision-making in mine safety and design — with minimal impact to production schedules.
ENHANCED STOPE ANALYTICS
The reconciliation and analysis of a stope relies on the quality of the data produced by the stope scan.
With CMS, the quality of a scan is limited by the location of the static scanner and the size and shape of the cavity—resulting in poor point density and shadowing that can occlude over-break.
In comparison, Hovermap flies beyond the brow, into the stope, to capture data consistently in the range of ten to twenty thousand points per square meter and without shadowing.
High resolution point clouds deliver several benefits. Analytics conducted on a rich point cloud data gives engineers greater confidence in the final stope volume for reconciliation of production tonnes or for backfill.
Over- and under-break can be calculated with greater certainty, plus there is better interpretation of the mechanism by which it occurred. Discontinuity traces and structural planes within a stope can be identified by geotechnical engineers, which previously was not possible given CMS coverage and quality limitations.
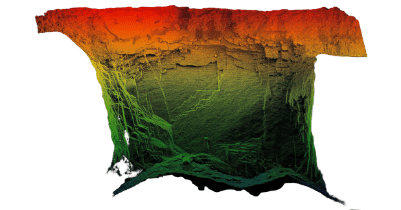
ACCURATE BACKFILL MONITORING
Mining operations backfill stopes to meet a variety of requirements, but most commonly to control dilution and stability within a mining area.
Monitoring of backfill material used for engineering purposes requires a high degree of detail to confirm the correct placement of the material within the stope, to ensure the design is correctly followed and to calculate the correct batch volume.
SAFER HANG-UP INSPECTIONS
Drawpoint hang-ups in both stoping and caving mines pose a serious safety hazard to the personnel attempting to clear them, and cause unplanned delays to production.
Common clearing methods are blasting and hosing with water to dislodge the material blocking the drawpoint. Scanning the drawpoint with Hovermap gives miners a clear view of the blockage and facilitates a targeted management approach.
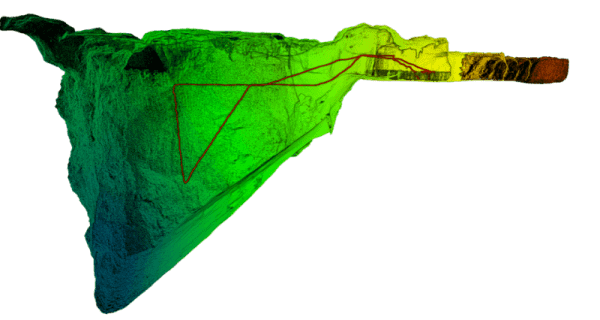